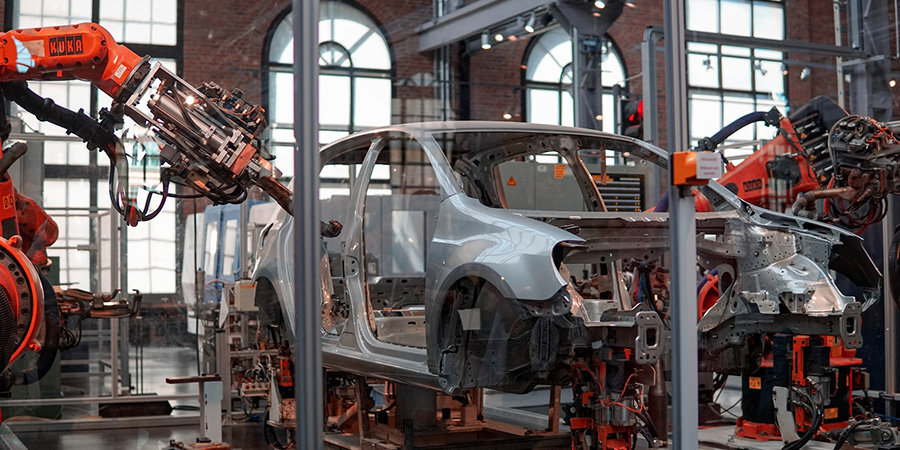
There's probably a smartphone in your pocket. Or maybe it's on your desk, next to a pen or some paper. As a matter of fact, everything in your room, smartphone included, is likely the outcome of a long, global process - all to get a product from the factory to the shipping line and, eventually, to you.
If you think about it, anything you use is engineering, says Dr. Jimmy Gandhi, Associate Dean of the university's Tseng College and a faculty member in the Smart Manufacturing certificate program. Whether it's the laptop you use, the clothes you wear, the house you live in, the car you drive - it's all manufacturing and supply chain.
You bought it off the shelf, he goes on, “but a lot happened behind the scenes to produce that product and get it there.
Thousands of small steps, in fact, beginning with materials acquisition, moving on to manufacturing, and leading, ultimately, to distribution and sale.
And manufacturing, it just so happens, is in the midst of a revolution. A new, smarter factory is emerging, and it's impacting the entire operations cycle from supplier to consumer.
What is smart manufacturing?
Instead of relying on trial and error, a smart factory employs a network of sensors to compile useful information: whether a system is optimal, for instance, or even working at all. Companies can then use this massive trove of data to make better decisions.
Through smart manufacturing, a company can anticipate failure and make iterative improvements on its production lines and supply chains. And thanks to advancements in sensor technology, this is all possible in real time, right as a product or technology is being manufactured or transported.
And it's not just sensors, either. Smart manufacturing is an ecosystem of technologies, from the internet of things to augmented reality to predictive analytics.
The obvious advantage of this, beyond massive savings in time and cost, is the ability to continuously refine systems - not after failure, but right away.
With smart manufacturing, calculations can now be done on much larger amounts of data, which are completely outside the range of human capabilities, says Gandhi. What this allows us to do is predict and refine processes on an ongoing basis.
To illustrate his point, Gandhi refers to the aerospace company Airbus:
They're now incorporating sensors in the fuselage and wings of new aircraft. Once the sensors are integrated, Airbus can use the data to predict when the structure is going to fail. It's pretty important in an airplane, he laughs. You don't want your wing to have an issue mid-flight.
But this example, he reminds me, is operational - what happens after a product leaves the manufacturing space. The same is true of a factory, however. Sensors, as in the aircraft, indicate an impending failure or reduced performance. Computers then process the data, which leads, eventually, to a decision point: what to fix, improve or stop altogether.
In the past, you needed a supercomputer to collect and process such huge amounts of data, says Gandhi. But now, just look at the power you have in your computer, or even your smartphone or tablet. It's cheap and fast, which means more accessible.
Boeing, BMW, Siemens, Amazon, and many others already employ smart manufacturing. But they're not alone. Numerous small to midsize companies are now making the transition from traditional to smart manufacturing. And to help, they're banking on a number of new, cutting-edge programs, such as CSUN's Certificate in Smart Manufacturing.
Not only is this program delivered fully online, but it's only ten months from start to finish. In that time, learners get hands-on experience with the same software and technologies used by industry. They also study the key fundamentals, from supply chain management and artificial intelligence to machine learning and data analysis.
With this certificate, graduates can join larger firms - in the aerospace or automotive industries, for instance - or help smaller ones integrate smart manufacturing principles and technologies into their processes.
An urgent demand for talent.
A growing skills gap is slowing hiring efforts nationwide, however. Companies need engineers with a smart manufacturing education. But few such professionals exist in today's market.
Just how urgent is the need?
According to a recent Deloitte study, 53 percent of all smart manufacturing jobs are vacant. The problem, in other words, is not a lack of positions, but a lack of people - well-trained people.
Consider also the field's expected economic output: $3.9 to $11.1 trillion a year by 2025. Coming as no surprise, the industry is aggressively recruiting a new workforce, in large part to capitalize on this enormous opportunity.
But it's not all economics, says Gandhi. There's a massive consumer benefit as well.
It's simple, he says. The consumer can expect a better product.
Considering smart manufacturing? Learn more at go.csun.edu/aboutSM.
Follow Us
Thinking about taking a class this semester? There’s still time to enroll through CSUN’s Open University with no admission process, just opportunity! Open to everyone. Flexible online and in-person.
— CSUN Tseng College (@csun_tseng) August 25, 2025
Enroll today: https://t.co/RYc6LL5ZRO#CSUN #CSUNOpenUniversity #Fall2025 pic.twitter.com/SpEfYgqELK